Erektor, Gripper, Chips, EPB, VSM und TBM. Nein, hier geht es nicht um einen neuen Rapsong. Vielmehr handelt es sich um wesentliche Bestandteile des modernen Tunnel- oder Schachtbaus. Die Zeiten, in denen der mit Spitzhacke bewaffnete Arbeiter am Ende des Arbeitstages fast ohnmächtig ins Bett fiel – vorausgesetzt er überlebte seine lebensgefährliche Schicht – sind lange vorüber.
Über 200 Meter lange und über 1.000 Tonnen schwere Tunnelbohrmaschinen (TBM) haben seinen Platz eingenommen. Die Ergebnisse sind überzeugend. Erst am 1. Juni 2016 Jahren wurde nach einer 17-jährigen Bauzeit der mit 57,1 Kilometern längste Tunnel der Welt, der Gotthard-Basistunnel, eröffnet. Ohne neueste Tunnelbau-Technik unvorstellbar.
200 Meter-Wurm frisst sich durch den Berg
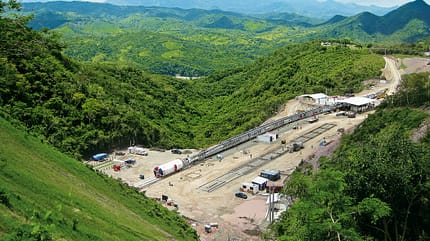
Einfach formuliert ist die eine Tunnelbohrmaschine ein gerne über 200 Meter langer Wurm aus Stahl, der sich sich durch den Berg frisst. Am Kopfende sitzt eine rotierende Scheibe mit bis zu 19 Meter Durchmesser (zum Vergleich, das entspricht einem sieben Stockwerke hohen Wohnhaus), in die rund 60 Rollenmeißel aus hochlegiertem Stahl eingelassen sind. Allein die Meißel haben einen Durchmesser von 43 Zentimetern. Auf jeden einzelnen wirken Kräfte bis zu 32 Tonnen.
Durch die Abrollbewegung der Scheibe brechen einzelne Felsstücke, sogenannten Chips, aus dem anstehenden Gebirge und rutschen über integrierte Kanäle zum Zentrum der Maschine. Dort fallen sie durch den trichterförmigen Muckring auf das Förderband, das sie aus dem Tunnel nach draußen transportiert. Alternativ werden schienengebundene oder gleislose Fahrzeuge für den Abtransport genutzt. Ihre über 5700 PS bringen große Tunnelbohrmaschinen rund 1,7 Meter pro Stunde (41 Meter am Tag) voran.
Unterschiedliches Gestein, unterschiedliche Techniken
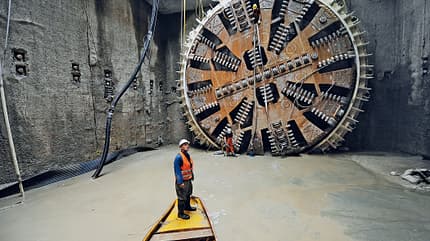
Da nicht jeder Untergrund gleich ist, gibt es unterschiedliche Vortriebstechniken für den Tunnelbau. Ob unter einem Fluss, einer Meerenge oder durch einen Berg – die Geologie, also der Baugrund, ist entscheidend für die Wahl der Vortriebstechnik. Wasserdrücke von über 15 Bar sind bei Flussuntergrabungen keine Seltenheit. Zum Vergleich: In einem normalen Autoreifen sprechen wir von rund 2,5 Bar.
Daher werden in weichen, bindigen Böden Vortriebsmaschinen mit Erddruckstützung (EPB) eingesetzt. Hier dient ein Erdbrei aus abgebautem Material als plastisches Stützmedium. Dies ermöglicht den nötigen Ausgleich der Druckverhältnisse an der Ortsbrust (Fläche, an der der Materialabbau stattfindet), verhindert ein unkontrolliertes Eindringen des Bodens in die Maschine und schafft die Voraussetzung für einen schnellen und weitestgehend setzungsfreien Vortrieb.
Fertiger Tunnel dank Tübbingverfahren
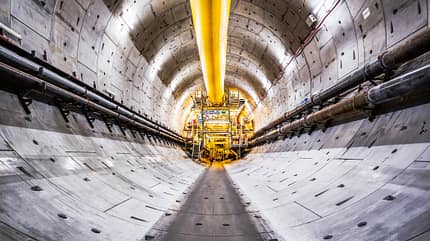
Besonders sehenswert ist das Ergebnis einer TBM, die zugleich das Tübbingausbauverfahren mit einzelnen Betonfertigteilen nutzt. Die einzelnen Segmente (Tübbinge) werden durch den fertiggestellten Bereich des Tunnels transportiert und direkt hinter der Tunnelbohrmaschine mit einem fernbedienbaren Kranarm, dem so genannten Erektor, zu geschlossenen Ringen verbunden. Das Resultat ist ein nahezu fertiger Tunnel direkt hinter dem Bohrkopf. Für den Vortrieb nutzt die TBM hydraulische Vortriebspressen, die sich am zuletzt gebauten Tunnelring abstützen.
Ähnlich geht es bei der Gripper-TBM zur Sache. Sie kommt beim Tunnelvortrieb im Hartgestein zum Einsatz. Mithilfe von direkt hinter dem Bohrkopf installierten Felssicherungsmaßnahmen können sie auch in brüchigen geologischen Formationen eingesetzt werden. Der Name Gripper leitet sich von den seitlich ausfahrbaren Hydraulikzylindern ab, die die Gripperplatten oder Gripperschuhe fest an die zuvor ausgebrochenen Tunnelwand pressen. Gewaltige Vortriebszylinder stützen sich anschließend an der verspannten Grippereinheit ab und drücken so den Bohrkopf an die Ortsbrust.
Mit dem Hammer auf Nummer sicher
Doch was, wenn sich mitten in einem Berg die Geologie ändert und das Gestein härter wird oder sich plötzlich ein Hohlraum auftut? Damit solche Situationen nicht unerwartet auftreten, kommt unter anderem bei einem der größten Unternehmen im Tunnelbohrsegment Herrenknecht die ISP (Integrated Seismic Prediction) zum Einsatz. Auf die Tunnelwand wird ein pneumatisch angeregter Hammerschlag ausgeübt. Etwaige Hindernisse reflektieren die dadurch entstandene Raumwelle auf unterschiedlich Weisen, die von einem System registriert und kategorisiert werden. Zudem können Vorauserkundungsbohrgeräte bis zu 100 Meter voraus Informationen sammeln.
Senkrecht durch weiche Böden und Festgestein
Was in der Horizontalen geht, schaffen moderne Schachtabsenkanlagen, genannt VSM (Vertikal Shaft Sinking Machine), auch in der Vertikalen. Diese Maschinen sind in weichen und standfesten Böden bis zu einer Druckfestigkeit von 80 MegaPascal sowie unter Grundwasser einsetzbar. Bis zu fünf Meter beträgt die Teufleistung pro Schicht. Wie schon die großen Tunnelbohrmaschinen graben die VSM nicht nur ein bis zu 150 Meter tiefes Loch, sie hinterlassen auch einen nahezu fertigen Schacht.
Eine moderne bis zu 185 Tonnen schwere Schachtabsenkanlage besteht aus zwei Hauptkomponenten, der Schachtbohrmaschine und den Absenkeinheiten. Die mit einer Kraft von bis zu 80.000 Newtonmeter arbeitende Schachtbohrmaschine wird in das Startrohr abgelassen und mit drei Maschinenarmen fest im Schacht fixiert. An einem Schrämausleger ist eine drehende, mit Rundschaftmeißeln bestückte Fräswalze befestigt, die sich mit maximal 80 Umdrehungen pro Minute dreht. Sie löst und zerkleinert den anstehenden Boden an der Schachtsohle. Der Schrämausleger ist teleskopier-, schwenk- und rotierbar. Dadurch kann sukzessiv der gesamte Schachtquerschnitt plus Überschnitt (zwischen 4,5 und 18 Metern) abgebaut werden. Der Abtransport des Abraums erfolgt hydraulisch über eine Tauchmotorpumpe zur Separationsanlage an der Oberfläche.
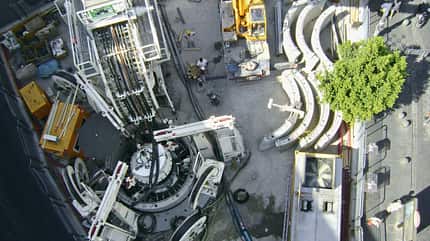