Kolben aus dem 3-D-Drucker, das klingt fast wie Science-Fiction, dennoch ist es ein Hightech-Verfahren, an das Porsche große Erwartungen hegt. Und das bereits in der Praxis erprobt wird. 3-D-Druck ist ja nun nichts Neues, bei Porsche entstehen etwa bereits Rennsportsitze oder Ersatzteile für den Klassikbereich im 3-D-Druck. Doch nun haben erste im additiven 3-D-Druck entstandene Kolben Belastungstests auf dem Motorenprüfstand absolviert.
Das Verfahren hat viele Vorteile, erläutert Frank Ickinger aus der Porsche-Antriebsvorentwicklung. "Was bisher nicht ging, wird machbar", schwärmt der Ingenieur. "Durch das Fertigungsverfahren können wir die Kolbenstruktur optimieren, einen Kühlkanal integrieren und das Gewicht des Kolbens um zehn Prozent senken."
Es wirkt wie Zauberei
In einem 3-D-Drucker der schwäbischen Firma Trumpf schweißen mehrere Laser Metallpulver Schicht für Schicht zu Kolben zusammen. Fünf Kolben eines GT2-RS-Motors (102 mm Bohrung) passen in den Drucker vom Typ TruPrint 3000. Das Metallpulver kommt vom Kolbenhersteller Mahle, es besteht aus einer Leichtmetalllegierung, die auch für konventionell gefertigte Gusskolben verwendet wird. Obwohl der Prozess rund zwölf Stunden dauert – 1200 einzelne Schichten schmelzen dabei die Laser zusammen – ist der Prozess insgesamt 30 Prozent schneller als herkömmliche Verfahren, bei denen erst Guss- oder Schmiedewerkzeuge hergestellt werden müssen.
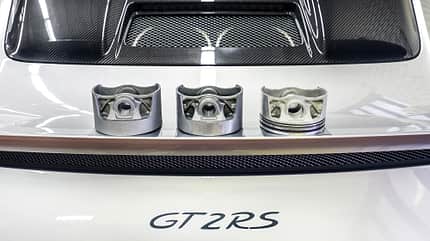
Die additive Fertigung durch das sogenannte Laser-Metal-Fusion-Verfahren bietet den Ingenieuren zudem konstruktive und fertigungstechnische Möglichkeiten, von denen sie früher nicht zu träumen wagten, weiß Ickinger.
So ist es möglich, bionisches Design einzusetzen, Material nur dort aufzutragen, wo ein Kraftfluss stattfindet. Das spart Gewicht. Mit zehn Prozent Einsparung sei man auf der sicheren Seite geblieben. "Unsere Simulationen zeigen, dass bis zu 20 Prozent Gewichtseinsparung möglich sind. Höhere Drehzahlen durch geringere oszillierende Massen sind so möglich. 300 Umdrehungen bedeuten im Fall des GT2 RS 30 PS mehr."
Eine weitere Besonderheit der neuen Kolben ist der hinter den Kolbenringen integrierte Ölkanal zur zusätzlichen Kühlung des thermisch besonders belasteten Bereichs um die Kolbenringe. Im Inneren des Kolbens läuft ein ringförmiger Tunnel, Öl fließt durch und führt Wärme ab. "Das wäre beim Schmieden oder Gießen von Kolben nicht darstellbar", sagt Motoreningenieur Ickinger. Bei Versuchen zeigte sich, dass dadurch die Temperatur im Bereich um die Auslassventile um 20 Grad sank.